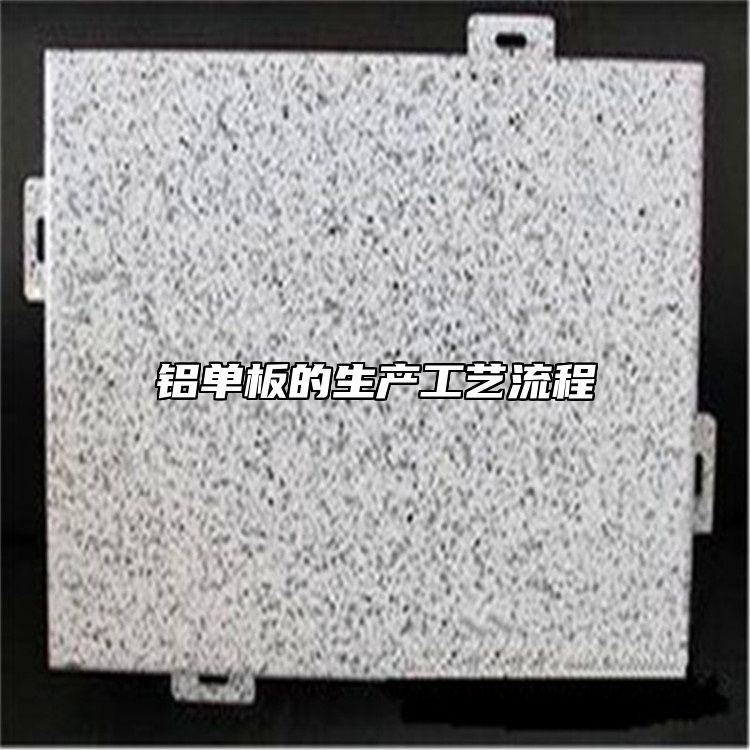
The production process flow of aluminum veneer
Abstract: Aluminum veneer, as a commonly used building decoration material, has a certain degree of complexity in its production process. This article will provide a detailed explanation of the production process of aluminum veneer from four aspects: material preparation, processing technology, coating technology, and quality inspection.
1、 Material preparation
In the production process of aluminum veneer, material preparation is the first step. The main raw material for aluminum veneer is aluminum alloy sheet, and the preparation work mainly includes material selection, cutting, and pretreatment. 1. Material selection: Select suitable aluminum alloy sheets based on usage requirements and design needs. Generally speaking, commonly used aluminum alloy sheets include aluminum manganese alloy sheets, aluminum magnesium alloy sheets, and aluminum silicon alloy sheets, each with their own characteristics and suitable for different environments and applications. 2. Cutting: The selected aluminum alloy sheet is cut according to the process requirements, usually using a shearing machine or cutting machine to obtain aluminum veneer blanks that meet the size requirements. 3. Pre treatment: Surface treatment of aluminum veneer blanks, including cleaning, removal of oxide film, and decontamination processes, to ensure smooth coating and processing of the next step.
2、 Processing technology
Aluminum veneer processing technology is a key link in the production process, mainly including cutting, bending, punching, and welding processes. 1. Cutting: According to the design requirements, cut the pre treated aluminum veneer into the desired shape and size. The commonly used cutting processes include laser cutting, CNC cutting, and stamping. 2. Bending: The aluminum veneer sheet after cutting is bent using a dedicated bending machine to achieve the desired shape and angle as designed. The accuracy and precision of the bending process directly affect the quality and appearance of the finished product. 3. Drilling: According to the design drawings, drill holes on the aluminum veneer for subsequent installation and fixation. The punching process can be achieved through equipment such as punching machines, drilling machines, or laser cutting machines. 4. Welding: Welding treatment is carried out at the parts that need to be connected. Common welding methods include argon arc welding and resistance welding. The reasonable selection of welding processes and proficiency in operating techniques are crucial for ensuring welding quality.
3、 Painting process
The coating process of aluminum veneer is to enhance its surface corrosion resistance, decorative effect, and weather resistance. The painting process includes steps such as primer coating, topcoat coating, and baking paint curing. 1. Primer coating: Apply primer coating to the processed and cleaned aluminum veneer to enhance its corrosion resistance and adhesion. Primer is usually sprayed, and attention should be paid to uniform application and appropriate thickness. 2. Topcoat coating: After the primer dries, apply the topcoat coating to achieve the decorative effect and color requirements. Topcoat coating can use different colors and types of paint according to design requirements, such as spray coating, roller coating, or brush coating. 3. Paint curing: After the coating is completed, place the aluminum veneer in the paint baking room for baking, so that the paint can cure and adhere to the surface of the aluminum veneer. The temperature and time of baking paint need to be adjusted according to the type and thickness of the paint to ensure the quality of the paint film and surface smoothness.
4、 Quality inspection
Quality inspection is an important step in the production process of aluminum veneer, aimed at ensuring that the product meets specifications and requirements. This mainly includes several aspects such as appearance inspection, size testing, and performance testing. 1. Appearance inspection: Inspect the appearance quality of aluminum veneer, including surface flatness, color difference, scratches, and bubbles. Evaluate whether the appearance quality of aluminum veneer meets the requirements through visual inspection and inspection under lighting conditions. 2. Dimensional inspection: Use specialized measuring tools to inspect the dimensions of aluminum veneer, including parameters such as length, width, and thickness. Ensure that the dimensional accuracy and tolerances of the aluminum veneer meet the design requirements. 3. Performance testing: Testing the performance of aluminum veneer, including indicators such as strength, hardness, and corrosion resistance. Determine whether the aluminum veneer meets the corresponding technical requirements through laboratory testing and physical and chemical performance analysis.
5、 Summary:
This article elaborates on the production process of aluminum veneer in detail, introducing it from four aspects: material preparation, processing technology, coating process, and quality inspection. Understanding the production process of aluminum veneer can better understand its characteristics and advantages, providing reference and guidance for practitioners in related industries. In practical applications, appropriate aluminum alloy materials and processes should be selected according to specific needs and environmental conditions to ensure the expected product quality and engineering results.